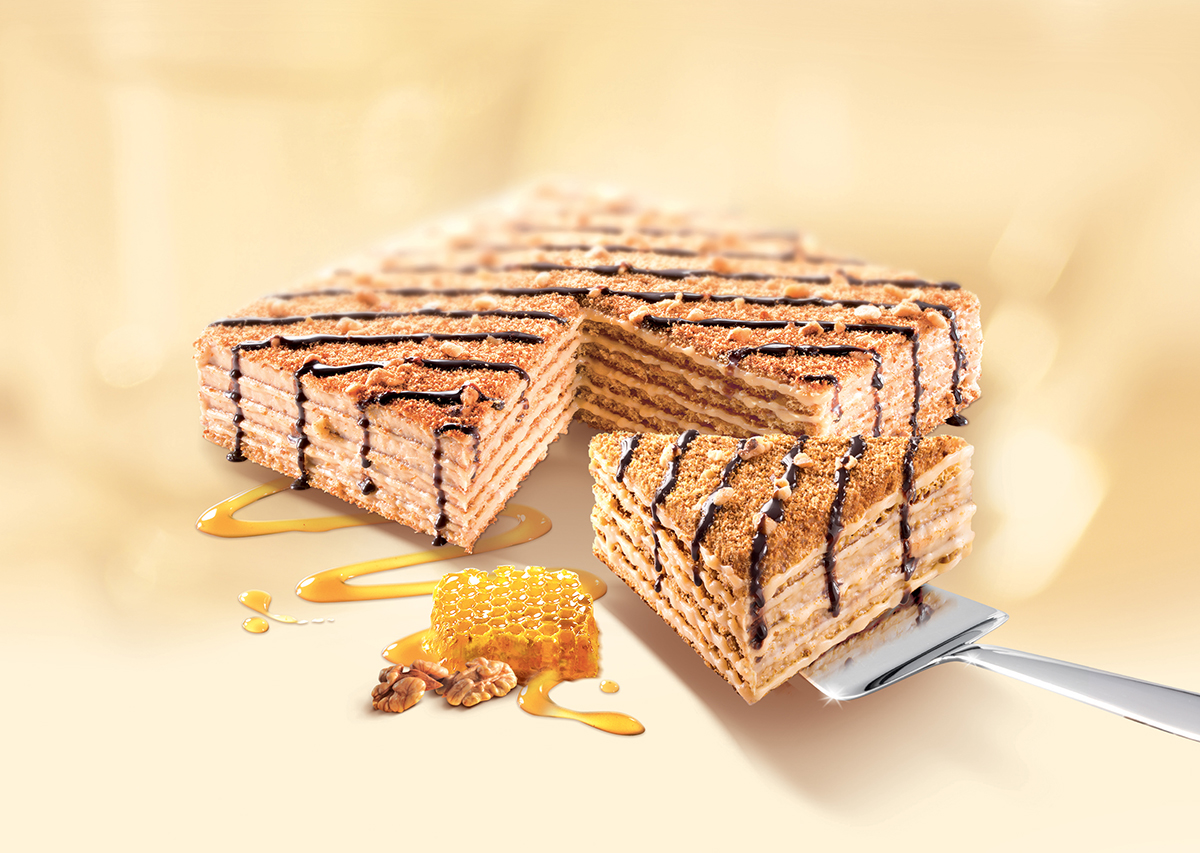
Marlenka
Branch: food
Activity: sweets production
Number of software users: 30
Number of employees: 180
Year of implementation: 2010
Reasons for Dialog 3000S implementation:
Need for a tool for process management of company activities, this is what happened when a bakery manufacture turned into a manufacturing company. Precondition for this brave deed was also to choose a good information system with a long tradition which can handle a continuous machine production of bakery products, where each of them has to have its own birth certificate. In tough competition the best was selected – Dialog 3000S, as it had similar experiences from different uses.
Implemented modules:
The first implemented module was Purchasing and sales for record of warehouse management, cash sales to distributors, economic module including attendance and salaries. After moving to new production premises Production management with production dispatching (monitoring doses of individual ingredients) was implemented as well as Laboratory, e-warehouse and data collection from machines.
Characterisation:
From certification perspective the most important module is used for monitoring individual batches of ingredients entering the production of production team shifts and keeping expiry dates. Thanks to a proper use of this module Marlenka company has achieved the biggest level of certification in food manufacturing.
All this is supported by data collection – communication with production line, where line registers on-line values in IS, it is possible to track back production parameters according to batch number (temperatures in furnice, production time, etc.)
Cash register and IS Dialog environment support the business in company cafe and recently opened customer centre.
This cooperation takes form of regular service and consultation visits, when IS is modified and supplemented according to user requirements. Recently, the company has used funds from Job Centre and had its employees trained in the area of new trends in IS.